Posts tagged ‘automation’
What You Need To Know About Automated Guided Vehicles
Automated Guided Vehicles (AGVs) are reshaping the way industries operate, offering a bounty of benefits for those ready to embrace the future of automation. Learn how autonomous machines increase efficiency across various sectors and how you can introduce them into your operations with little or no infrastructure required.
Understanding AGVs
AGVs are self-operating mobile robots guided by sensors, cameras, and predefined routes or markers. They transport goods, materials, or products within a facility without human intervention. AGVs can come in various forms, from small, compact robots to larger, more specialized machines, depending on the application’s specific needs.
Six Ways AGVs Boost Efficiency
- Improved Workflow and Material Handling: AGVs excel in repetitive and time-consuming tasks like material transport. By deploying AGVs in a facility, companies can significantly reduce the time and effort spent moving goods from one location to another.
- Precise and Consistent Operations: AGVs operate with remarkable precision. They can follow predefined routes within millimeter accuracy, ensuring that materials are delivered to the correct location every time. This level of consistency minimizes errors and reduces the need for rework, ultimately improving overall efficiency.
- 24/7 Operations: Unlike human workers who need breaks and rest, AGVs can operate around the clock. This continuous operation capability means production can continue uninterrupted, increasing output and efficiency.
- Scalability: As businesses grow, their material handling needs often increase. AGV systems are easily scalable by adding more robots to the fleet. This flexibility ensures companies can adapt to changing demands without significant disruptions or delays.
- Safety and Reduced Downtime: Safety is a top priority in any industrial setting. AGVs use advanced safety features such as collision avoidance systems and emergency stop capabilities to help protect employees and minimize downtime due to accidents.
- Data-Driven Optimization: AGVs use sensors and cameras that collect valuable data about operations, including traffic patterns, cycle times, and resource utilization. This data helps identify areas for optimization and continuous improvement.
Applications Across Industries
AGVs are versatile and find applications across various industries:
- Manufacturing: AGVs transport materials to assembly lines, reducing idle time and increasing production rates.
- Warehousing and Distribution: AGVs efficiently move goods within warehouses, helping to meet the demands of e-commerce and same-day delivery services.
- Healthcare: AGVs are used in hospitals to transport medications, supplies, and linens, allowing healthcare professionals to focus on patient care.
- Automotive: AGVs help automotive plants deliver parts, support assembly lines, and transport finished vehicles.
- Agriculture: AGVs can automate crop harvesting and transportation in large-scale farming operations.
Toyota’s Automated Forklifts
Toyota’s Automated Forklifts rely on LiDAR-based natural features navigation, ensuring precise positioning and load delivery with accuracy tolerances of as little as half an inch.
What is the benefit for you? You won’t have to undergo the hassle of reorganizing your facility’s infrastructure or dealing with a complex setup process. We create a detailed map of the designated work area for the Toyota Center-Controlled Rider Automated Forklift, and the equipment takes care of the rest effortlessly.
Toyota currently offers two Automated Forklifts.
- Center-Controlled Rider Pallet Jack: Constructed upon the dependable foundation of the Toyota Center-Controlled Rider Pallet Jack, the groundbreaking Toyota Center-Controlled Rider Automated Forklift leverages state-of-the-art environmental sensing to automate repetitive warehouse tasks. Employing advanced sensors for cutting-edge mapped-object detection combines Toyota’s renowned warehouse equipment reliability with cutting-edge automation technology. This synergy results in cost reduction and operational streamlining for your facility.
- Core Tow Tractor Automated Forklift: The Toyota Automated Core Tow Tractor uses an advanced AC Drive System, AC Drive Motor, and regenerative braking capabilities. This powerful tow tractor significantly enhances productivity and is the perfect solution for horizontal material transport and cart pulling within your facility. Furthermore, each AGV in the lineup harnesses the power of LIDAR-based natural features navigation, reducing the need for extensive infrastructure or intricate setup procedures.
Learn more about Toyota’s Automated Forklifts and see them in action here: https://www.youtube.com/watch?v=kqhoxPySs4M.
AGVs represent a paradigm shift in industrial automation, offering many advantages to businesses seeking to enhance efficiency. If you are ready to embrace the AGV revolution and unlock the full potential in your operations, contact our automation experts to schedule a free consultation today.
Order Picking Solutions: Ask the Expert Series
It is no secret that managing a warehouse or distribution center today is a challenge, primarily if you rely on manual processes. Adding order picking fulfillment technologies can help.
In this blog post, we continue our Ask the Expert Series with Toyota Material Handling Solutions’ Director of Sales and Marketing Anthony Spano. Anthony’s decades of experience in picking processes and technologies can help determine the best solution for your application. Today he explains six order picking technologies and the benefits of each one.
What are the benefits of order fulfillment technologies?
An automated order picking solution offers many benefits, but here are the big three:
- Increased efficiency
- Reduced picking errors
- Improved customer service
What are the different types of order picking solutions?
Here are the top six solutions companies are implementing today:
- Goods-to-person
- Voice picking
- Pick to light
- Put to light
- Put wall
- RF handheld scanners
What is goods-to-person order fulfillment?
Goods-to-person combines automated storage with accurate, ergonomic picking processes. With this system, products are automatically transported directly to the operator as needed, saving valuable travel time to retrieve the order.
What are the main benefits of goods-to-person order picking?
- Ideal for ergonomic picking
- Easily scalable to match growing demand or an increase in SKUs
- Produces a smaller footprint and uses less space than other order picking solutions
What is voice picking order fulfillment?
Voice picking is an easy-to-learn paperless order picking solution. With voice picking, an operator is equipped with a mobile device and a headset and given easy-to-understand voice prompts to tell them where to go and what to do.
What are the benefits of voice picking?
- Flexible and scalable solution
- Great for environments with many SKUs
- Keeps operators’ hands-free and focused on the task at hand
What is pick-to-light order fulfillment?
Pick to light, also called pick-to-light or PTL, is a light-directed warehouse picking technology. It provides accurate and efficient paperless picking, putting, and sorting.
What are the benefits of pick-to-light order fulfillment?
- A versatile solution for many applications
- Highly effective in zones with high pick volumes and dense pick faces
What is a put to light system?
A put to light system is like a pick to light system but reverse. Instead of order fulfillment, a put to light system replenishes stock.
What are the benefits of a put to light system?
- Very efficient for stock replacement
- Non-intrusive. Lights are typically mounted on shelving or carton flow rack placed above or below the designated put to light device.
What is a put wall system?
A put wall system handles a large volume of orders in a small footprint. We implement our Exacta® supply chain software suite as a complete solution or separate components in this system. It is also compatible with other software brands and is easily scalable.
What are the benefits of a put wall system?
- Paperless processing
- Smaller footprint than other systems
What are RF handheld scanners?
RF handheld scanners are an easy-to-install modular solution with access to data from anywhere in the world. We use the Exacta mobile platform to deliver the most critical information directly to the operators with this system.
What are the benefits of RF handheld scanners?
- Quickly and easily incorporate product images
- Supports multiple languages
There are many ways to use automated systems to increase efficiency and productivity. Click on these links to read about robotic palletizing, robotic order picking, and cube utilization, and stay tuned for future Ask the Expert blog posts.
Got questions about the process of optimizing your warehouse with Toyota? Click here to learn the first steps in the process, what is involved in the analysis, what you will get back from Toyota, who secures the permits, how much you need to be involved in the process, and more.
Ready to automate your warehouse or distribution center? Contact us today!
Robotic Order Picking: Ask the Expert Series
In this part of our Ask the Expert Series, Toyota Material Handling Solutions’ Director of Sales and Marketing Anthony Spano answers frequently asked questions about robotic order picking.
Anthony helps companies find the ideal mix of automation, software, and labor to optimize productivity and deliver fast, accurate fulfillment to match the speed of modern commerce. His expertise has helped hundreds of companies in Los Angeles County maximize cube utilization, increase throughput, and increase their bottom line.
What is a robotic order picker?
A robotic order picking system is an automated storage and retrieval system (ASRS). It harnesses the power of warehouse robots for 24/7 order fulfillment within a cubic layout.
What are the benefits of order picking robots?
- Increased on-time delivery
- Reduced stock losses and errors
- Increased customer satisfaction
- Improved space utilization
- Lower building/rental and labor costs
Which order picking system do you recommend?
AutoStore is our system of choice.
What is AutoStore?
AutoStore is an innovative storage solution that allows complete customization and flexibility. In the AutoStore system, bins are stacked vertically in a grid and retrieved by robots that travel on the top layer of the system.
Does AutoStore work if you have a complicated warehouse layout?
Yes. Because AutoStore robots travel on the top layer of the system, the grid can exist around columns, on the mezzanine, and even on multiple levels.
How does AutoStore work?
An AutoStore system contains four components: a structural grid, delivery robots, storage bins, and an operator port. Products live in bins within the dense aluminum grid. As a product is needed to fulfill an order, the system software and controls alert a robot to find the item’s bin.
How does the robot get to the bins on the bottom of the stack?
If the bin is beneath other bins, a robot stages the extra bins on top of the grid until it retrieves the desired container. It then takes that bin to the edge of the grid and delivers it to the operator fulfilling the order.
What happens to the bins on top of the grid after an order is retrieved?
As one robot delivers the bin, another AutoStore robot cleans up the staged bins on top of the grid by returning them to their original position.
Does the system get smarter with time?
Yes. As the order-picking process continues, the AutoStore system self-profiles. The bins with faster-moving products begin moving toward the top of the system, and bins with slower-moving products transition to the bottom.
How much space can you save with an AutoStore system?
In some cases, a company can increase storage capacity four-fold within the same footprint and unlock the true potential of storage floor space.
Is AutoStore a custom solution?
Yes, an AutoStore system is designed specifically for you. Each AutoStore is designed based on your operational needs, and we validate it through simulation backed by its control system.
Can I add AutoStore to my existing space?
Yes, AutoStore is easy to integrate into existing warehouses.
Can I use AutoStore if I have low ceilings?
Yes, AutoStore is fully customizable to fit any ceiling height.
What is the maximum lifting speed of an AutoStore robotic order picker?
An AutoStore robot has a maximum lifting speed of 5.2 feet per second.
What industries use AutoStore systems?
You can find AutoStore systems in grocery, retail, healthcare, e-commerce warehouses, third-party logistics centers, parts management facilities, and many other specialty industries.
Do you have any case studies to share?
Yes. We partner with Bastian Solutions, a Toyota Logistics company and a global AutoStore integrator. Click here to learn how they modernized Best Buy’s supply chain with advanced automation. You can also watch how they helped Puma increase capacity tenfold and boost productivity by twenty percent at their facility in Indianapolis.
Is 2022 the year you add robots and automation to your order picking process? Don’t tackle it alone. Let our experts with decades of experience help take your warehouse or distribution center to the next level. Contact us to get started today!
Ask the Expert Series: Robotic Palletizing
In this blog post, Toyota Material Handling Solutions’ Director of Sales and Marketing Anthony Spano answers frequently asked questions about robotic palletizing systems and solutions.
Anthony has a decade of expertise in maximizing cube utilization and increasing throughput by employing the ideal mix of automation, software, and labor. His superpower is using high-performance solutions to help companies optimize productivity and deliver fast, accurate fulfillment to match the speed of modern commerce.
What is a robotic case palletizer?
A robotic palletizer employs a robotic arm to pick, orient, and place individual products and arrange them into a single stack or load.
What are the benefits of a robotic palletizing solution?
There are numerous benefits of using a palletizing robot, but I will stick to the top five.
- Increased productivity: Palletizers eliminate manual labor for unitizing products. They are much more efficient, lift heavier loads, and perform faster.
- Better product handling: Since palletizers are automated machines, their movements are pre-programmed to function without damaging the product.
- Small and flexible: Palletizing robots typically have a smaller footprint than other solutions, offer greater flexibility, and fit in extremely tight spaces.
- Improved workplace safety: Robotic palletizers eliminate many workplace hazards typically associated with manual labor like falling, tripping, and muscle strains from repetitive actions.
- Reduced operating costs: Most operations can save money by increased productivity, low product damage, and reduced labor costs.
How does a robotic case palletizer work?
A palletizing robot picks one or multiple cases from a conveyor system and places them on a pallet. The process continues layer by layer until the pallet is complete.
How does the palletizing robot know what to pick and place?
Pallet patterns, which can easily be changed or added, are programmed into the palletizing robot.
What is the function of an end-of-arm tool?
The end of arm tool can handle multiple types of containers simultaneously, regardless of their shape. It can pick up cases, bags, pails, bottles, batteries, cubes of scrap metal, plastic containers, and many other things.
Can a robotic palletizing solution handle different patterns and product types?
Yes. A robotic palletizer can handle one or more units according to pallet configuration and forms multiple layers on a pallet after picking the products off a conveyor.
Can a palletizing robot handle multiple feeds of different SKUs on the same line?
Yes. There are systems to send information to the robot to pick and place different SKUs on different pallets.
How much weight can a palletizing robot handle?
Robotic palletizing systems can typically handle up to 2,200 pounds.
How fast are palletizing robots?
For a single robot picking a single product, palletizing rates can vary anywhere from eight to thirty cases a minute, depending on stacking patterns and other requirements.
How long can a palletizing robot operate?
Unlike human labor, palletizing robots do not experience exhaustion or injuries. With proper maintenance, palletizers can reliably operate 24/7.
Can a robotic palletizing system and solution serve multiple lines?
Yes. One robotic palletizer can work between two or more packaging lines.
Can a palletizing robot perform secondary tasks?
Yes, some robotic palletizers have a vacuum, magnetic, or custom end-of-arm tools to give them the ability to perform additional tasks such as slip sheet dispensing, pallet placing, and wrapping.
Can a robotic palletizing system reverse its operation?
Yes. This feature is on robotic palletizers-depalletizers.
What industries typically use robotic case palletizers?
You can find palletizing robots in many industries, including food and beverage, life sciences, packaged goods, electronics, and more.
Are there pictures and videos available?
Yes, click here for pictures and videos of robotic palletizers in action.
Do you have other automated warehouse solutions?
Yes. Click here for tips on how to upgrade your warehouse for maximum efficiency.
Implementing a robotic palletizing system requires knowledge and planning. Let our team of storage and automation experts design a unique plan just for you.
If you are in Los Angeles County, contact us for a free consultation today.
What can Autonomous Mobile Robots do for you?
Have you wondered if you should utilize autonomous mobile robots in your warehouse or distribution center? Well, you are not alone.
The use of autonomous mobile robots to improve efficiency in warehouses and distribution centers is undoubtedly on the rise. A recent study found that investment in warehouse robotics increased by 57% in the first quarter of 2020. It is a clear sign of things to come.
In fact, according to an August 2021 report by Research and Markets, the global warehouse automation market will reach $30.99 billion in 2025, and experts predict there will be 50,000 robotic warehouses by the same year.
So, you might ask yourself how autonomous mobile robots can benefit your warehouse, what you can automate, and what these robots can do?
If you are thinking about implementing warehouse automation and robots, here are answers to frequently asked questions about what robots can do for you.
What can autonomous mobile robots do in a facility?
Autonomous mobile robots can handle hundreds of tasks every day and thousands of orders every week. Here are some of the tasks robots can complete in a warehouse:
- Picking
- Packing
- Batching
- Sorting
- Transporting
- Security
- Inspections
How are autonomous mobile robots used in warehouses and distribution centers?
- Autonomous mobile robots can replace conventional conveyors with portable and affordable plug-and-play systems to save space.
- Autonomous mobile robots can transport heavy objects to reduce employee strain and injury.
- Drones can conduct aerial inventory scanning, reach secluded areas in the warehouse, and inspect stock.
- Task robots can complete repetitive functions.
- Delivery robots can help with order picking.
- Palletizing robots can pick one or multiple cases and quickly and accurately place them on a pallet.
How does the Internet of Things (IoT) enhance robot functions?
- IoT sensors transform multiple warehouse devices into intelligent devices that communicate in real-time without human intervention.
- IoT connects and coordinates your distribution facility, so workers, robots, managers, and automated vehicles always know the location of items.
What are the benefits of autonomous mobile robots?
- Increased turnaround time
- Reduced costs
- Enhanced customer satisfaction
- Reduced labor and operational costs
- Reduced handling and storage costs
- Improved employee satisfaction
- Greater inventory control
- Optimized warehouse space
- Increased employee safety
- Reduced physical strain on employees
- Reduced amount of errors/returns
- Reduced employee injuries from repetitive tasks
What kind of equipment can you automate in a warehouse or distribution center?
- Forklifts
- Conveyors
- Pallet movers
- Shelving
- Local delivery vehicles
What kind of robots are popular to use in a warehouse?
- Mobile robots
- Drones
- Task robots
Warehouse automation and robots will continue to grow in the years ahead. Many companies in Los Angeles County begin with a warehouse management system, data collection, and inventory management.
Our systems and automation experts are available to guide you in your journey through warehouse automation. If you need help or advice, contact us today.
Upgrade your Warehouse for Maximum Efficiency
Distribution and fulfillment centers are always looking for ways to maximize operational productivity and efficiency. The current COVID-19 pandemic, increasing e-commerce sales, and a limited labor pool have only intensified the need for companies to get more done in a shorter amount of time. Learn how to upgrade your warehouse for maximum efficiency.
To help stay competitive in today’s environment, distribution and fulfillment centers often invest in automated warehouse solutions and robots to increase efficiency. Here are four steps to the warehouse automation process and the different types of warehouse robots and what they do.
- First, start simple. Many companies begin by adding equipment designed to move products more efficiently. For example, conveyors and carousels can increase productivity by reducing the time to get a product from point A to point B.
- Next, reduce redundant tasks. The next step is to simplify specific tasks and procedures with software, machine learning, and analytics. For example, software can analyze and batch orders so employees can make one trip to a specific area to retrieve orders instead of taking many trips throughout the day.
- Give your employees assistance. To automate further, look for ways to assist your employees with warehouse tasks and procedures. For example, Automated Storage and Retrieval Systems (AS/RS) can retrieve items and put them away, increasing productivity by reducing order picking time.
- Finally, automate repetitive procedures. Advanced warehouse automation can replace labor-intensive, repetitive functions. For example, Autonomous Mobile Robots (AMRs) can conduct inventory counts at predetermined times or intervals to allow employees to focus on more value-added tasks.
Here’s a look at the various types of warehouse robots and their specific functions:
- Articulated Robotic Arms
- Use: Automate order fulfillment tasks.
- Function: Moves items from pallets for picking, packing, and shipping.
- Example: Robotic limbs with multiple joints.
- Automated Guided Vehicles (AGVs)
- Use: Automate simple transportation paths.
- Function: Transports items from point A to point B.
- Examples: AGVs on tracks. AGVs paired with sensors to avoid obstacles.
- Automated Guided Carts (AGCs)
- Like AGVs, but carry smaller loads.
- Automated Storage and Retrieval Systems (AS/RS)
- Use: Automate the retrieve and return process.
- Function: Retrieves goods for shipment. Returns items to their proper storage locations.
- Examples: Cranes that pick orders. Shuttles that move on fixed tracking systems.
- Autonomous Mobile Robots (AMRs)
- Use: Automate simple transportation paths. Automate inventory process. Automate teaching simple tasks.
- Functions: Transports inventory from point A to point B. Conducts inventory. Teaches and guides associates through a task.
- Examples: AMRs with maps and sensors. AMRs paired with RFID-tagged products. AMRs with collaborative abilities.
- Goods-to-Person technology (G2P)
- Use: Automate the delivery of items to picking stations.
- Function: Delivers products to areas where employees are waiting to fill orders.
- Example: Automated and software-driven systems requiring minimal human interaction.
- Unmanned Aerial Vehicles (UAV)
- Use: Real-time inventory visibility.
- Function: Provides inventory visibility in warehouses equipped with RFID technology.
- Example: Drones.
Are you interested in implementing an automated warehouse system in your distribution and fulfillment center? Our warehouse systems experts are eager to help. They know all the ins and outs of getting the most out of your warehouse space and design. Contact us today to get started.
What Can Automated Forklifts Do for You?
Every company wants to improve efficiency, lower costs, and streamline operations. Handling repetitive tasks with automated forklifts is often the easiest way to accomplish all these things simultaneously.
Our material handling experts help companies in the manufacturing, warehousing, and distribution industries find cost–effective ways to automate repetitive tasks. The main goal is to free up personnel to perform more value-added functions.
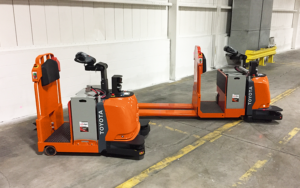
Toyota Center-Controlled Rider & Core Tow Tractor
Last month, Toyota unveiled two new automated forklifts to help companies streamline tasks and reassign duties: a new Center-Controlled Rider Automated Forklift and Core Tow Tractor Automated Forklift.
Here are ten features and benefits of Toyota’s new automated forklifts:
- Simple integration: Easily integrate Toyota’s latest automated forklifts into your existing operations; they require little or no additional infrastructure or setup.
- Cost–effective: Toyota’s automated forklifts have no ongoing subscription or service fees.
- Peace of mind: Backed by Toyota 360 Support, including a 4-hour guaranteed emergency response time and a 2-year parts warranty.
- Leading technology: Toyota’s new automated forklifts feature Light Detection and Ranging (LIDAR) Natural Features Navigation developed by Bastian Solutions, a Toyota Advanced Logistics Company.
- Extreme accuracy: Toyota automated forklifts position and maneuver with an accuracy tolerance range as narrow as a half-inch.
- Object detection: Advanced sensors on Toyota’s automated forklifts slow or stop the vehicle when an unmapped object is in its path.
- Ease of service: Toyota’s automated forklifts feature AC Drive Motors, self-adjusting electric disc brakes, and a one-piece, lightweight service access cover.
- Flexibility: Easily switch between automated and manual modes for versatility and control.
- High Load Capacity: Toyota’s Center-Controlled Rider Automated Forklifts have a load capacity of up to 7,000 pounds.
- High Tow Capacity: Toyota’s Core Tow Tractor Automated Forklifts have a towing capacity of 10,000 pounds.
Our automation experts are eager to help you find ways to automate your warehouse to decrease operating costs, improve efficiency, and free up personnel to perform more value-added tasks. Contact us today for a free consultation!
Finding the Bright Side of Automation
Automation is a hot topic. More companies are increasingly turning to robotics and technology to automate processes to increase efficiency and create safer working environments.
Definition of Automation
So, what exactly is automation? Automation refers to any automated process that reduces or eliminates the need for human involvement.
After reading the definition, it makes sense to think automation will result in lost jobs. While automation will eliminate some low-wage repetitive jobs, it will also help create jobs in other areas. For example, companies need technicians to perform maintenance on robots, conveyors, and other automation-related equipment, thereby creating more high-paying technician jobs.
What Does the Future Hold?
A report by the World Economic Forum titled “The Future of Jobs 2018” estimates that artificial intelligence and robotics will create nearly 60 million more jobs than it destroys by 2022. The report finds that while automation technologies and artificial intelligence could see 75 million jobs displaced, another 133 million new roles may emerge, which equals 58 million new jobs created by 2022.
Some redundant roles that will decline include data entry, accountants, delivery drivers, and factory workers. The bright side is new jobs will emerge like robotics engineers, innovation professionals, solution designers, and people and cultural specialists.
Not everyone has to worry about being affected by automation. Oxford University researchers predict that 47% of American jobs may face automation over the next two decades. It means 53% of jobs will be completely unaffected.
This shift in the job market can be a positive change if you look at it this way: Some workers may lose their low-paying, often pain-inducing, repetitive jobs, but they’ll have plenty of opportunities to pursue entirely different careers in new emerging positions. And don’t worry; robots won’t take over jobs that require human interaction, like doctors and teachers. However, manufacturing, transport, and administration employment are likely to decline.
Do you want to learn more about how automation can help your company? Contact us for more information.
Can Automation Create Engaged Employees?
Automation is getting a lot of attention lately. We are fascinated with the rise of self-driving cars and robots delivering packages right to our homes. Plant and warehouse managers who have utilized automation in some form or another have seen the benefits. Let’s explore how automation can create a safer environment and more creative, satisfied, and engaged employees.
Automation can reduce or eliminate repetitive, often pain-inducing, physical tasks.
According to the Bureau of Labor Statistics in 2016, back-related musculoskeletal disorders accounted for 38.5 percent of all work-related musculoskeletal disorders. Many of these injuries are caused by lifting heavy objects.
Pallet Positioners are easy, low-cost products to help employees eliminate strain on their backs. These products lift, rotate, and place heavy pallets in the ideal position for loading and unloading. Utilizing pallet positioners also helps employees perform their jobs faster to boost productivity.
Bastian Solutions, a Toyota Advanced Logistics Solutions company, recommends the Southworth PalletPal™ 360. The PalletPal™ includes a platform that raises and lowers as you add and remove boxes and a turntable to make the process easier, faster, and more ergonomic. Click here to watch a video of the Southworth PalletPal™ in action and learn more about its features.
Automation can allow you to reassign workers to safer job duties.
Robots are more expensive than pallet positioners and AGVs, but these productive additions to your facility can take over all aspects of loading and unloading pallets. It’s an investment that can eliminate the potential of employee injury and free up employees to perform other essential tasks.
Bastian Solutions offers several robotic palletizing solutions to handle pallets, slip sheets, and more. Click here to learn more about this cutting-edge technology.
Reassigning employees can lead to higher employee satisfaction.
With the addition of automation and industrial robots, employees can work in new ways. Their new duties might include managing the robots doing the work or engaging in higher-level, more creative tasks. These new opportunities often result in empowered, more satisfied employees.
Contact us for a free consultation to learn how to help you achieve lower worker compensation claims, lower turnover, higher productivity, and higher employee satisfaction.
ProMat 2019 Recap: The Latest Material Handling Equipment & Technology
ProMat 2019 has officially wrapped. Over 45,000 manufacturing and supply chain professionals were in attendance for the industry’s largest conference, held April 8-11th at Chicago’s McCormick Place convention center.
This year’s theme was “Find Your Wow,” focusing on the latest innovations in material handling technology, warehouse automation, and robotics. With over 1,000 exhibitors, 100+ seminars, and hands-on demonstrations, there was a lot to see and do at the event. In this post, we’re recapping just a few of the highlights from this incredible event.
ProMat 2019 Highlights:
Toyota 3-Wheel Hydrogen Fuel Cell Forklift

Toyota introduced an all-new piece of material handling equipment at the conference, a 3-wheel hydrogen fuel cell forklift that will go into production later this year. This option is a great zero carbon emissions alternative to traditional internal combustion forklifts.
Karim Lakhani’s’s Opening Keynote Panel Session

In his keynote, Karim Lakhani, a professor at Harvard Business School and the session’s panelists, representatives from Cargill, Everledge, and Intel, highlighted how companies are currently using blockchain technology today and discussed the potential it has for the industry.
MHI Innovation Award Winners Announced
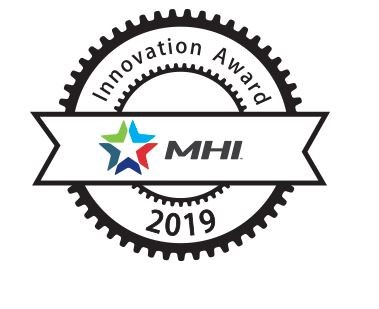
The winners of the MHI Innovation Awards were announced at ProMat 2019 Industry Night. Pick2Pack from CMC srl won in the Best New Product category. RightHand Robotics won Best Innovation of an Existing Product for their updates to their product, RightPick. For the Best IT Innovation category, KNAPP won with redPilot.
Forklift to Robots Seminar

Richard Cole of Bastian Solutions, Troy Donnelly, and Alan Dotts of Toyota Material Handling covered the strategies for identifying if your business could benefit from automation. They provided practical how-tos for evaluating technology solutions, from palletizing robots to the latest automated guided vehicles (AGVs) capable of stacking and storing pallets.
Contact Us for more information on ProMat2019 and Toyota’s exciting products and programs.